Superheated Steam Drying: A Brief Introduction
Sakamon Devahastin
Department of Food Engineering
King Mongkut’s University of Technology Thonburi
126 Pracha u-tid Road, Bangkok 10140, Thailand
Tel.: +662 470 9246; Fax: +662 470 9240
E-mail: sakamon.dev@kmutt.ac.th
1. Introduction
Superheated steam drying (SSD) involves the use of superheated steam in a direct (convective) dryer in place of hot air, combustion, or flue gases as the drying medium to supply heat for drying and to carry away the evaporated moisture. Any direct or direct/indirect (e.g., combined convection/conduction) dryer can be operated as a superheated steam dryer, at least in principle. The technology involved is more complex and hence this conversion is not simple, however (Mujumdar, 2000).
One of the obvious advantages of SSD is that the dryer exhaust is also steam, albeit at lower specific enthalpy. If air infiltration is avoided (or minimized to an acceptable level), it is possible to recover all of the latent heat supplied to the SSD by condensing the exhaust steam or by mechanical or thermal compression to elevate its specific enthalpy for reuse in the dryer. Since SSD will necessarily produce steam equal in amount to the water evaporated in the dryer, it is necessary to have a useful application for this excess steam in the process plant. If this steam is used elsewhere, the latent heat recovered is not charged to the SSD, leading to a net energy consumption figure of 1000-1500 kJ/kg water removed for SSD compared with 4000-6000 kJ/kg water removed in a corresponding hot air dryer. Thus, reduced net energy consumption is a clear advantage of SSD. In addition to the ability to recover all of the latent heat supplied to the dryer there are also other advanthages of SSD as summarized below (Mujumdar, 2000; Kudra and Mujumdar, 2002; Devahastin and Suvarnakuta, 2004).
Generally, no oxidative reactions (e.g., enzymatic browning, lipid oxidation or aerobic degradation of vitamins) are possible in SSD due to lack of oxygen. This is especially beneficial when enzymatic browning is not desirable, e.g., during drying of apple and banana.
SSD can help inactivating microorganisms, both of the toxin-producing and non-toxin-producing types, due to its normally high-temperature environment, even during an early stage of drying. It is also known that moist heat (in this case superheated steam) is more effective in inactivating microorganisms than dry heat, i.e., hot air. A combination of drying with other thermal treatments, e.g., blanching, deodorization, pasteurization and sterilization, is also possible.
Another noted advantage of SSD is that, for certain foods or vegetables, the porosity of the products dried in superheated steam is higher than that dried in hot air. This is due to the evolution of steam within the product, which decreases bulk density of the product while enhancing its rehydration characteristics. This feature is especially attractive for the instant food as well as confectionery industries.
Higher drying rates (comparing with hot air drying) are possible in both constant and falling rate periods of SSD, depending on the steam temperature. The higher thermal conductivity and heat capacity of superheated steam leads to higher rates of surface moisture removal above the so-called inversion temperature. Below the inversion temperature drying in air is faster. In the falling rate period the higher product temperature in SSD (over 100°C at 1 bar) and lack of diffusional resistance to water vapor lead to faster drying rates. Also, it is known that many products that form casehardened skin in rapid drying do not form such water-impermeable skins in SSD.
Accompanying the above advantages are such limitations as the complexity of the system. No leaks can be allowed since noncondensables cause problem with energy recovery by compression or condensation. Feeding and discharge of SSD must not allow infiltration of air. The product itself may bring in noncondensables. Start-up and shutdown are more complex operations for an SSD than for an air dryer. In addition, since feed enters at ambient temperature, there is inevitable condensation in the SSD before evaporation begins. This adds about 10-15% to the residence time in the dryer. At 1 bar operating pressure drying begins at a product temperature of 100°C in the constant rate period when surface water is being removed. Alternatively, a pre-heater is needed for the feedstock (or the drying chamber itself).
Since the temperature of the product undergoing SSD is relatively high, being at the steam saturation temperature at the dryer operating pressure during the constant rate period and even higher during the falling rate period, some products may undergo undesirable physical or chemical transformations. In such cases a low-pressure operation is desirable (Devahastin et al., 2004).
If the steam produced in the dryer is not needed elsewhere in the process, the energy-related advantages of SSD do not exist. Also, steam cleaning may not always be a simple task. The chemical composition of the condensate must be carefully evaluated. Cost of the ancillaries (e.g., feeding systems, product collection systems, exhaust steam recovery systems) is typically much more significant than the cost of the steam dryer alone. This extra cost may be offset by the enhanced product quality, which is especially the case for the food and biotechnological industries, however.
2. Basic principles of superheated steam drying
A simple schematic sketch of a superheated steam drying system is shown in Figure 1. Saturated steam from a boiler or a steam generator is heated up in a heater (steam superheater) and becomes superheated steam. Drying takes place through a direct contact between superheated steam and the product to be dried. As mentioned earlier, the exhaust of the dryer is also steam, albeit at lower specific enthalpy. Steam is recirculated and reheated in a closed loop; only the amount of steam that corresponds to the amount of evaporated water is removed from the closed loop and used either directly or indirectly after its energy being recovered via a heat exchanger. The closed loop of SSD implies that emissions coming from the drying product are not emitted to the environment but are included in the condensate; toxic or expensive organic liquids can therefore be recovered more easily than in the case of hot air drying.
There are other drying technologies that are similar to the system described above. In that case the evaporated water itself becomes available as steam after some time necessary to vent the originally present air from the system. This type of system is widely used in wood drying applications.
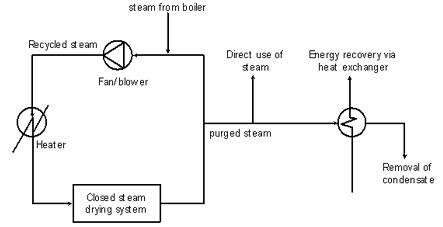
Figure 1. A schematic sketch of a superheated steam drying system
Superheated steam has heat transfer properties superior to air at the same temperature. Since there is no resistance to diffusion of the evaporated water in its own vapor, the drying rate in the constant rate period is dependent only on the heat transfer rate. The convective heat transfer coefficient, h, between steam and the solid material surface can be estimated using standard correlations for interphase heat transfer. Neglecting sensible heat effects, heat losses and other modes of heat transfer, the rate at which surface moisture evaporates in steam is given simply by:
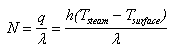
where N is the evaporation rate, Tsurface is the drying surface temperature which corresponds to the saturation
temperature at the dryer operating pressure and Tsteam is the temperature of the superheated steam and l is the latent heat of vaporization. In hot air drying, Tsurface = Twet-bulb and hence at
lower drying temperatures, DT is
higher in air drying but h is lower. It turns out that these counter-acting
effects lead to the phenomenon of inversion; a temperature beyond which
superheated steam drying rate is greater than hot air drying rate (see Figure
2). This is confirmed
experimentally as well as numerically for water as well as several organic
solvent systems (superheated vapor drying). It is observed that the inversion
temperature is in the order of 160o-200oC for evaporation
of water in superheated steam for various flow configurations and flow regimes,
e.g., laminar/turbulent boundary layer flows, impinging jet flows, free
convective flow over complex geometries. Strictly speaking, the inversion
temperature is defined only for surface moisture evaporation and not for
internal moisture removal although some researchers do not make this
distinction clear when reporting their results. However, the values of the
inversion temperature calculated based only on surface moisture evaporation
rates are obviously not the same as those calculated based on the combined
constant rate and falling rate drying rates (Suvarnakuta et al., 2005)
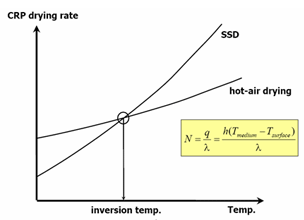
Figure 2. An inversion phenomenon
It is observed that, often, drying rates in the falling rate period are also higher in superheated steam drying relative to air drying. Here, the mechanisms responsible are quite different. In superheated steam drying the product temperature is higher and hence moisture mobility is greater. Note that in steam environment casehardening or skinning may not occur thus eliminating a possible impediment to intensive drying. The product is likely to be more porous as well.
3. Classification and selection of superheated steam dryers
Figure 3 classifies superheated steam dryers based on their operating pressure (Mujumdar, 2000). The product temperature necessarily exceeds the saturation temperature of steam at the corresponding operating pressure. So, for products that may undergo undesirable physical transformations (e.g., melting) or chemical transformations (e.g., hydrolysis) at elevated temperatures, a low-pressure operation is desirable.
As noted above, any direct dryer (e.g., flash, fluidized bed, spray, impinging jet, conveyor dryers), in principle, can be converted to a superheated steam dryer. Thermal efficiencies can be improved and the unit size reduced by supplying a part of the heat indirectly (e.g., by conduction or radiation). Note that the inversion temperature is lowered in the presence of indirect heat supply, which is a further benefit. For example, in the presence of an appropriate radiant heating, the inversion temperature dropped from 250°C to 170°C for a specific case reported in the literature.
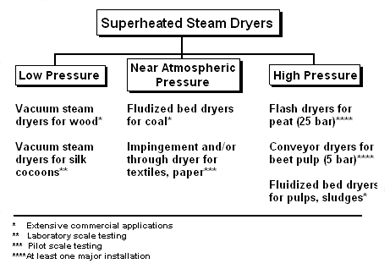
Figure 3. Classification of superheated steam dryers based on their operating pressure
It is not necessary to
always operate an SSD above the inversion temperature to benefit from the
advantages of SSD, however. Aspects other than higher drying rates or lower
energy consumption, such as quality or safe operation, may dominate the
selection procedure in most cases. For relatively low-value products (e.g.,
sludges, meat by-products, hog fuel) that are readily combustible in hot air and
dried in large tonnages, the reduced net energy consumption in SSD is
particularly advantageous since this also reduces the environmental emissions
of greenhouse gases (e.g., CO2) as well as toxic gases (NOx, SOx).
However, the excess steam produced must have a viable application in or near
the process.
Table 1 summarizes the
key factors contributing to the feasibility of superheated steam drying. Both
product- and process-related factors must be considered. Laboratory testing is
required before proceeding with any decision to consider superheated steam
drying. The dryer types that have been successfully tested at pilot scale
and/or commercialized for at least some products include flash dryers, with or
without an indirect heating of dryer walls; fluidized bed dryers, with or
without immersed heat exchangers. Other less common types of dryer include
spray dryers (operated at near atmospheric pressures, for drying of whey);
impinging jet dryers (for newsprint, tissue paper, at small scale; for textiles
at commercial scale); conveyor dryers; agitated bed dryers; packed bed/through
circulation dryers and rotary drum dryers.
Table 1. Factors contributing to the feasibility of superheated steam drying
Factor |
Description of impact |
Product-related factors |
Low temperature sensitivity |
To avoid higher steam temperature, more expensive vacuum systems are required |
High moisture content |
Since the latent heat of the moisture can be recovered with SSD, the bigger the portion it represents, the greater will be the efficiency improvement |
High thermal resistance |
Higher surface temperature with SSD reduce heating and drying times |
High sensitivity to oxidation |
Lack of oxygen with SSD improves product quality |
Undesirable taste or aroma |
SSD strips more of the acids which contribute to bitter tastes |
High product values |
Drying time reductions provide biggest inventory cost savings with higher value products |
Process-related factors |
Other uses of steam available |
Energy consumption for the process is small and the capital costs are minimized |
Environmental emissions from dryers |
SSD provides easier recovery of solvents and particulates |
Combustion/explosion hazards |
Lack of oxygen significantly reduces fire/explosion hazards |
Expensive source of thermal energy |
Thermal energy savings with SSD will offset greater the energy costs than with waste fuels (e.g., hog fuel) |
References
Devahastin, S., Suvarnakuta, P., 2004 “Superheated Steam Drying of Food Products,” pp. 493-512, in A.S. Mujumdar (Ed.) Dehydration of Products of Biological Origin, Science Publishers, Enfield, USA.
Devahastin, S., Suvarnakuta, P., Soponronnarit, S., Mujumdar, A.S., 2004, “A Comparative Study of Low-Pressure Superheated Steam and Vacuum Drying of a Heat-Sensitive Material,” Drying Technology, 22, pp. 1845-1867.
Kudra, T., Mujumdar, A.S., 2002, Advanced Drying Technologies, Marcel Dekker, New York.
Mujumdar, A.S., “Superheated Steam Drying – Technology of the Future,” pp. 115-138, in S. Devahastin (Ed.) Mujumdar's Practical Guide to Industrial Drying: Principles, Equipment and New Developments, Exergex, Brossard, Canada.
Suvarnakuta, P., Devahastin, S., Soponronnarit, S., Mujumdar, A.S., 2005, “Drying Kinetics and Inversion Temperature in a Low-Pressure Superheated Steam Drying System,” Industrial & Engineering Chemistry Research, 44, pp. 1934-1941. |